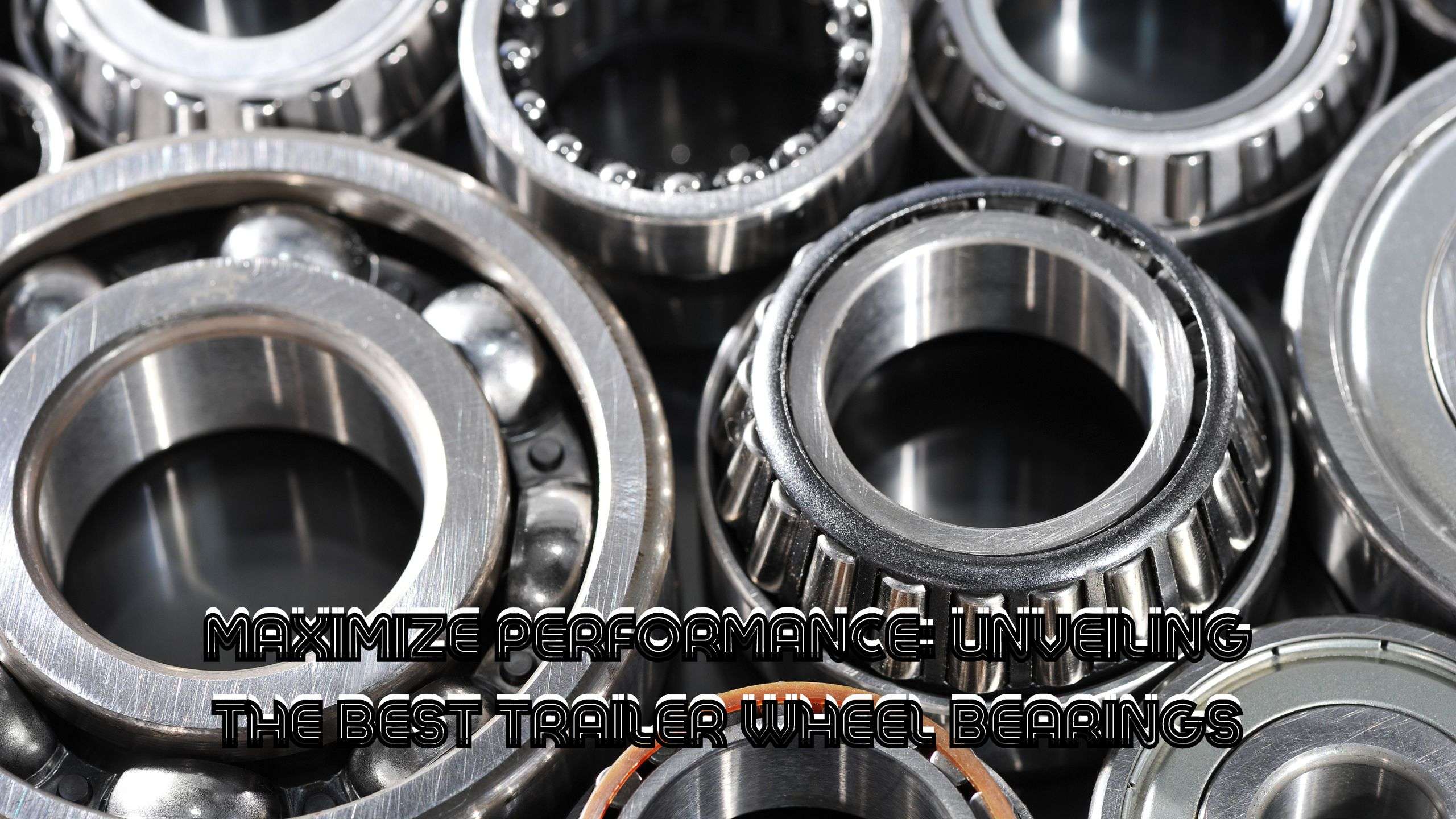
Maximize Performance: Unveiling the Best Trailer Wheel Bearings
Understanding Trailer Wheel Bearings
In the world of heavy-duty and commercial vehicle equipment, trailer wheel bearings hold a certain prominence. These small but mighty components play a critical role in the functionality and efficiency of a trailer’s wheels and axles, ensuring smooth and safe travel (HowStuffWorks).
The Basic Functions of Wheel Bearings
Trailer wheel bearings carry out three main functions: they support the weight of the trailer and its cargo, allow the wheels to spin with minimal friction, and help to keep the wheels in alignment. These functions are crucial to the overall performance of the trailer, whether it’s hitched to a small private vehicle or a large commercial truck.
The role of the wheel bearings is to ensure that the wheels rotate smoothly and freely, reducing the amount of energy required to move the trailer. This reduction in friction also helps to minimise wear and tear on the tyres and other components, extending their lifespan and reducing maintenance costs.
Common Types of Wheel Bearings
When it comes to trailer wheel bearings, there are several types to choose from, each with its own characteristics and benefits. Here, we will delve into the most common types, including roller bearings, tapered roller bearings, hub assemblies with integrated bearings and races, needle and cylindrical roller bearings, and flanged bearings.
Tapered roller bearings, in particular, are a popular choice for trailers. They are designed to handle heavy loads and withstand the stress of towing, making them ideal for heavy-duty and commercial applications.
These bearings are typically made of steel, which is both durable and capable of withstanding heavy loads and vibrations. This durability ensures that the bearings can perform their function effectively, even under the most demanding conditions.
When selecting wheel bearings, it’s important to consider the specific needs of your trailer. Factors such as the weight of the trailer and its cargo, the type of terrain it will be travelling on, and the frequency of use can all influence the best choice of wheel bearings.
By understanding the basic functions and common types of trailer wheel bearings, you can make an informed decision when choosing the right bearings for your trailer. This understanding, coupled with regular maintenance, can help to maximise the performance and longevity of your trailer’s wheel bearings.
The importance of regular maintenance
When it comes to trailer wheel bearings, regular maintenance is not just recommended; it’s crucial. Proper upkeep of these components can prevent unnecessary wear, damage, and even dangerous situations on the road. In this section, we will discuss the signs of worn or damaged bearings and the importance of regular inspection and maintenance.
Signs of worn or damaged bearings
It’s essential for us to know the signs of worn or damaged trailer wheel bearings. Recognising these symptoms early can prevent further issues and ensure safe and smooth towing. Signs of compromised bearings include unusual noises, excessive heat, uneven tyre wear, and wheel wobbling.
If the trailer wheels are loose or spin with a wobble, it’s a clear indication that the bearings must be serviced or replaced (felling trailers). Another red flag is if the trailer wheel hubs are too warm to hold your hand in place after towing for a short distance. This could indicate a bad bearing that requires lubrication or replacement.
Regular inspection and maintenance
Regular inspection and maintenance of trailer wheel bearings are vital to prevent potential issues and ensure safe towing. It is recommended to check the bearings at least once a year or every 10,000 miles, and to repack them with fresh grease as needed. Bearings should be replaced or repacked with grease every 12,000 miles or at least once a year, whichever comes first. Neglecting regular maintenance can lead to bearing failure and costly repairs.
When checking trailer wheel bearings, there should be a very slight amount of play in the wheel, typically 1/8-inch or less (Felling Trailers). Greasing the bearings at least once a year or every 10,000 miles, whichever comes first, helps to prevent damage and ensures the smooth operation of the wheels.
Paying attention to these details can significantly extend the life of your trailer wheel bearings and enhance the overall performance of your trailer. For more information on maintaining other trailer components, check out our articles on trailer brake controllers, trailer lights and wiring, and trailer leaf springs.
Performing wheel bearing maintenance
In order to ensure the longevity and performance of your trailer wheel bearings, regular maintenance is crucial. This maintenance should include checking the bearings for wear and lubricating them as needed.
Checking wheel bearings for wear
It’s important to check your trailer’s wheel bearings on a regular basis. Doing so enables you to identify any signs of wear or damage early, preventing potential breakdowns and costly repairs down the line (felling trailers).
When checking the bearings, there should be a very slight amount of play in the wheel, typically 1/8-inch or less. If the wheels are loose or spin with a wobble, it’s a sign that the bearings need to be serviced or replaced.
Another indicator of potential bearing issues is overheating. If the trailer wheel hubs are too warm to touch after towing for a short distance, you may have a bad bearing that requires lubrication or replacement.
We recommend replacing or repacking your trailer wheel bearings with grease every 12,000 miles or at least once a year, whichever comes first. Regular inspections and maintenance can prevent bearing failure and save you from unnecessary expenses.
Lubricating wheel bearings
Regular lubrication is vital for the smooth operation of your trailer wheel bearings. Bearings should be greased at least once a year or every 10,000 miles, whichever comes first.
Re-greasing your wheel bearings helps keep them properly lubricated and prevents premature failure. It’s a good practice to have the wheel bearings of your trailer inspected and serviced at least once a year or every 12,000 miles. This regular maintenance can help identify early signs of wear or damage and prevent costly repairs or breakdowns on the road.
Proper maintenance of your trailer wheel bearings is a key part of ensuring your trailer’s performance and safety. By regularly checking for wear and lubricating the bearings, you can keep your trailer in top shape for all your towing needs. Be sure to check out our other guides on trailer maintenance, including tips on trailer brake drums, trailer leaf springs, and trailer safety chains.
Choosing the Right Wheel Bearings
When it comes to optimising the performance of your trailer, selecting the right wheel bearings is crucial. The right set of bearings not only ensures smooth operation but also significantly extends the life of your trailer’s wheels.
Factors to consider
Choosing the best trailer wheel bearings often depends on a variety of factors. These include the type of trailer, the load it carries, the terrain it traverses, and how frequently it’s used. Furthermore, you need to consider the maintenance requirements of different bearings.
Ideally, trailer wheel bearings should be replaced or repacked with grease every 12,000 miles or at least once a year, whichever comes first (eTrailer). Ignoring regular maintenance can lead to bearing failure and expensive repairs.
Also, the bearings should be greased at least once a year or every 10,000 miles, whichever comes first, to prevent damage and ensure smooth wheel operation (Camping World Blog). Neglecting to grease wheel bearings can lead to excessive heat buildup, bearing failure, and potentially a trailer wheel coming off while driving.
Picking Quality Wheel Bearings
When choosing trailer wheel bearings, it’s vital to prioritise quality over cost. High-quality bearings may cost more upfront, but they often provide better performance and longevity, making them a more cost-effective choice in the long run.
It is recommended to use high-quality trailer wheel bearing grease that is specifically formulated for high-temperature applications and provides long-lasting protection against water and corrosion. This type of grease can help prolong the life of your bearings and ensure they function efficiently under various conditions.
Remember, the safety and performance of your trailer are directly linked to the quality of its components. Therefore, investing in high-quality wheel bearings is a decision that pays for itself over time.
For a comprehensive guide to other trailer components, feel free to explore our articles on trailer hitch locks, trailer brake controllers, trailer lights and wiring, and trailer safety chains.
Addressing common wheel bearing issues
When it comes to trailer wheel bearings, certain common issues can arise that require immediate attention. These problems, if not addressed promptly, can lead to significant damage and potential safety risks. In this section, we’ll discuss two such issues: overheating and premature failure, as well as contamination and corrosion.
Overheating and premature failure
One of the most common issues encountered with trailer wheel bearings is overheating, which can lead to premature failure. Excessive heat can cause the grease inside the bearings to break down, leading to premature wear and damage (Tow-Max). If the trailer wheel hubs are too warm to hold your hand in place after towing for a short distance, you may have a bad bearing that requires lubrication or replacement.
One way to check for bad trailer wheel bearings is to jack up the trailer and spin the wheel by hand. If the wheel does not spin freely or if you hear any grinding or scraping noises, it may be a sign of bad bearings.
Another indication of bad trailer wheel bearings is excessive play or movement in the wheel. If you can wiggle the wheel back and forth or side to side, it may be a sign that the bearings are worn out and need to be replaced.
Contamination and corrosion
Contamination and corrosion are other common problems that can affect the performance and lifespan of trailer wheel bearings. Exposure to water, dirt, and road salt are just a few of the causes of these problems.
Contamination can occur when foreign substances, such as dust or dirt, enter the bearing. This can cause abrasion and wear, reducing the efficiency and lifespan of the bearing. Regular inspection and cleaning can help to prevent contamination and ensure the longevity of your trailer wheel bearings.
Corrosion, on the other hand, is a chemical reaction that can occur when the bearings are exposed to moisture and oxygen. This can lead to rust and deterioration, which can significantly impact the performance of the bearings. To prevent corrosion, it’s important to ensure that the bearings are properly sealed and lubricated.
By understanding these common issues and taking proactive steps to address them, we can ensure the optimal performance and longevity of our trailer wheel bearings. Regular inspection, proper maintenance, and timely replacement of worn or damaged bearings are key to preventing these issues and maximising the performance of your trailer. Visit our articles on trailer safety chains and trailer brake controllers for more information on maintaining your trailer’s optimal performance.
Investing in Bearing Protectors
To extend the lifespan of the trailer wheel bearings and enhance their performance, investing in quality bearing protectors is a smart move. These specialised devices offer numerous benefits and can significantly help in maintaining the overall health of your trailer’s wheel bearings.
Benefits of Bearing Protectors
Bearing protectors not only safeguard your wheel bearings from the damaging effects of dirt, water, and road debris, but they also help in ensuring consistent lubrication. They can be a useful addition to your regular maintenance routine, assisting in prolonging the life of your bearings and preventing premature wear and tear.
One of the most common issues with trailer wheel bearings is a lack of lubrication, leading to premature wear and failure. Bearing protectors can mitigate this problem by maintaining a steady supply of grease for the bearings, helping them to function smoothly and efficiently.
Additionally, bearing protectors can also provide a clear indication of when it’s time to add more grease to your bearings. This can help in preventing over-lubrication, which can be just as detrimental to your bearings as under-lubrication.
Selecting and Installing Bearing Protectors
When choosing bearing protectors, it’s crucial to pick a product that matches the size and specifications of your trailer’s wheel bearings. You can find these details in your trailer’s owner’s manual or on the manufacturer’s website.
One of the products we recommend is the Trailer Bearing Buddies, which are bearing protectors with dust caps that have a 45mm diameter and include a grease overflow hole. They are sold in sets of two and are known for their high-quality performance.
Installation of bearing protectors is usually a straightforward process and can be done using basic hand tools. However, if you’re not confident in performing this task, it’s best to seek the help of a professional mechanic to ensure proper installation.
Investing in bearing protectors is a small step that can go a long way in maintaining the performance and longevity of your trailer wheel bearings. Combined with regular inspection and maintenance, bearing protectors can help you avoid costly and time-consuming repairs down the line.
For more information on wheel bearing maintenance and other trailer-related topics, don’t hesitate to explore our other articles on trailer hitch locks, trailer brake controllers, and trailer lights and wiring.
Author

I am Rahatul Ashiq Tamal. Another author of Muscle Trailers. Muscle Trailers is a well-known trailer brand in Sydney, Melbourne & Adelaide
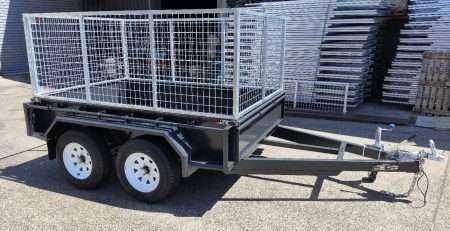
How to Mount a Spare Tire on Your Trailer: A Simple Step-by-Step Guide
Trailer service centers receive over 1 million phone calls and 1.3 million emails each year about trailer maintenance problems....
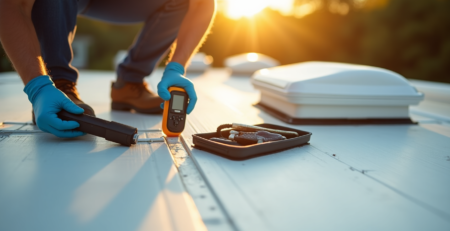
How to Fix RV Roof Leaks: Simple Roof Leak Detection Guide for Beginners
Did you know DIY RV roof repairs can cost under $50? But undetected leaks could lead to substantially higher repair...
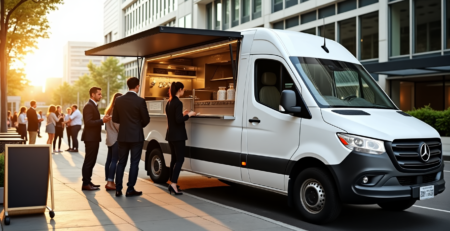
Starting a Food Truck Business in Australia: From Trailer Selection to Launch
The Australian mobile food market has evolved into a billion-dollar industry. This makes a food truck...